Note: While great efforts have been taken to provide accurate and complete information on the
pages of CPEP, please be aware that the information contained herewith is considered a work-in-progress for this thesis project. Modifications and changes related to the original building designs and construction methodologies for this senior thesis project are solely the interpretation of Christopher
Ankeny. Changes and discrepancies in no way imply that the original design contained errors or was flawed. Differing assumptions, code references, requirements, and methodologies have been incorporated into this thesis project; therefore, investigation results may vary from the original design. |
Building Statistics
General Information
Building Name: Abingdon Heights
Location: Falls Church, Virginia
Occupancy: Residential
Size: 536,000 SF
Number of Stories: 11
Construction Dates: July 10, 2006 – March 20, 2009
Construction Cost: $92,000,000
Delivery Method: Design-Bid-Build


|
Project Team
Owner: Equity Residential
dddddiiiiSunburst Hospitality Corporation
Architect: WDG Architecture
Structural Engineer: The SK&A Group
Geotechnical Engineer: Whitlock, Dairymple .............................................Poston and Assoc.
General Contractor: Donohoe Construction ........................................Company
MEP: WSP Flack and Kurtz
|
|
|
Architecture
The Falls Church high rise apartment tower possesses a distinctly post-modern look. Located at the edge of the courthouse district, Falls Church Tower serves as a transitional building between residential and commercial developments. The brick veneer and alternating recesses of the facade supplement the surrounding apartment complexes while the vertical glazed elements implement the sleek look of the inner district office buildings. Vista’s shape is defined by the contour of the road running just south of it. and provides a contrast to the curved façade of the hotel to the north. In addition to its visual contribution, Falls Chucrh Tower is only a mere ten minutes from the National Mall in Washington D.C. as well as six major parks making it a prime location for commuter living. |
|
Major National Model Codes
IBC 2006
IPC 2006
IMC 2006
NEC 2005
IFC 2006
IEEC 2006 |
|
|
|
Building Facade
The typical building facade consists of brick, mortar collector, building insulation, and 1/2" gypsum board with either an air barrier or self adhering sheathing behind the brick. Any visible concrete is used to emphasize the vertical elements of the building, specifically the glazed facade leading up to the penthouses as well as the gicular corner of the building that houses mechanical equipment inside the top ring. |
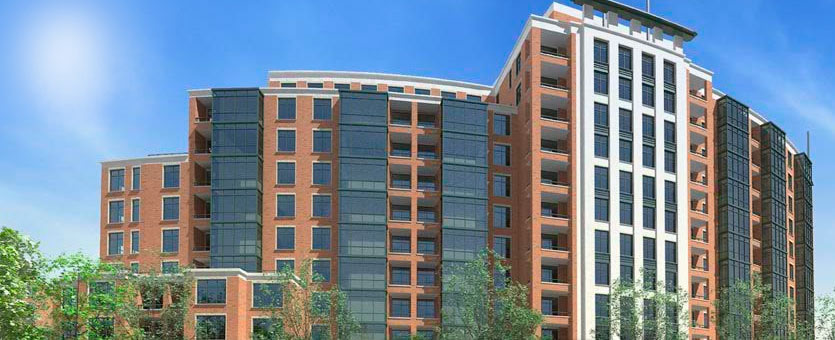
|
Sustainability
Still awaiting LEED Specifications
|
Roofing
The typical roof section is comprised of 7 in. thick, post tensioned concrete slab. The slab is coated with water proofing on top of which sits 1 in. of rigid insulation. Finally there is approximately 3 in. of stone ballast that covers everthing else. |
|
Construction
Construction of Falls Church Tower began with the demolition of the previous structure and the subsequent excavation of the basement 3 extension. The retaining walls were then poured followed by the spread footings, grade beams, and finally the slab on grade. Standard concrete pouring and shoring was implemented from level B3 to level 1. Installation of the post-tensioned slabs slowed down the construction process due to the method by which slabs are put in tension. The re-shoring had to be altered from floor to floor given the change in column sizes and orientation.
|
|
Structure
The structural system of the Falls Church high rise tower is comprised primarily of cast-in-place concrete. Exceptions include the cornices on the main roof which are constructed of W8x10, W8x15, and W8x21 steel beams. The foundation of the building is a three part system utilizing a 5 inch thick slab on grade with strap beams at key locations. The columns sit on spread footings of 5000 psi concrete and basements 1 through 3 have a retaining wall running the full length of the perimeter.
The gravity loads on the building are resisted by a flat plate system involving rectangular columns of 5000, 6000, and 8000 psi concrete. The columns are typically arranged in 24'x24' bays in a radial pattern with 6' spans for the corridor. The floor system is a one-way, post-tensioned slab with perpendicular tendons running between columns. The tendons themselves are primarily two and three strand tendons spaced four to five on center.
The lateral loads on the building are resisted by the moment frame composed of rectangular columns that alternate in direction. The columns range anywhere between 12 inches and 24 inches on the short face, and 12 inches to 48 inches on the long face. The typical reinforcing for a column will be #8 and #9 bars running both directions with some variation in bar size. |
|
Mechanical
The mechanical system was designed on the premise that the east half of the west half of the building would be treated as two separate towers. All mechanical equipment is located in the penthouse roof mechanical room. The main units are two 6000 CFM AAON RN series packaged AHU’s. Two condenser water pumps(primary and secondary) and one hot water pump are provided for both towers courtesy of Bell and Gossett. Two 2334 MBH Burnham V1112 fossil fuel boilers provide hot water for the 8000 gallon tank. Cooling is achieved by induced draft provided by BAC’s two cell cooling tower.
|
|
Electrical
Electrical service for Falls Church Tower is provided by Dominion Virginia Power Co. via 277/480V-3 Phase-4 Wire systems. These are, in turn, run from two D.V.P underground vault transformers. The source feeds into two 2500A switchboards which lead into two 1000KVA-480V Delta-208Y/120V dry type transformers. These supply two 2500A-3 Phase-4 Wire-120/208V plug-in busway risers which provide 400A and 600A service. In addition there is a 450kW, 575KVA-3Ph-4W-277/480V indirect diesel emergency generator located on level B1 with the rest of the equipment.
|
|
Lighting
The curved design of the building allows for more direct sun lightning throughout the day minimizing the use of artificial lighting. Typical artificial lighting for apartments takes the form of compact fluorescent pendent fixtures located in the kitchen, dining room, and bathrooms. Corridor lighting consists of wall mounted pendants that are also compact fluorescent.
|
|
Navigation
Occupants enter the building from either the lobby entrance located on the north face or from the main elevator in the parking garage beneath the building. Upon entering the lobby occupants are presented with two elevators. The corridor that runs past these elevators leads to the east and west ends of the building. The east end of the building provides an additional elevator. Both ends of the building have a stairwell that leads from the basement to the roof.
|
|
Fire Protection
Fire protection for the building is provided by the concrete framing which meets the required two hour rating.
|
|
|
|